Dans le contexte industriel et économique actuel, la capacité de l’industrie à innover et à rester compétitive repose sur l’optimisation permanente de ses activités, et notamment par sa transformation construite sur la valorisation d’une profusion de données trop souvent sous-exploitées.
Pour servir cet enjeu, Orange Business propose une offre complète de mise en place d’une infrastructure IT, associée à l’IoT et à l’OT, au service des opérations de production. L’objectif ? Sécuriser les processus et les opérateurs, optimiser et faciliter l'activité tout en la modernisant afin de rester compétitif.
En pratique et de manière simplifiée, cette infrastructure met en lien des données avec un réseau local sécurisé permettant de contrôler sa ligne de production en temps réel, d’agir plus rapidement en cas de panne ou de danger et même d’automatiser certaines tâches. L’infrastructure est flexible et scalable : elle peut être mise en place sur une partie de l’activité avant d’être utilisée progressivement plus largement, en fonction des besoins.
Pour regarder cette vidéo, vous devez consentir aux Cookies de notre partenaire Youtube Ces cookies permettent de partager ou réagir directement sur les réseaux sociaux auxquels vous êtes connectés ou d'intégrer du contenu initialement posté sur ces réseaux sociaux. Ils permettent aussi aux réseaux sociaux d'utiliser vos visites sur nos sites et applications à des fins de personnalisation et de ciblage publicitaire.
Les grands principes de l’industrie 4.0 illustrés par une mini usine
Pour rendre cette offre plus tangible et démontrer les bénéfices d’une telle transformation numérique, Orange Business a équipé une mini ligne de production. Cette usine connectée met en scène une chaîne de production de capsules de café, sécurisée et vertueuse, qui intègre des solutions de smart industries adaptées pour assurer une production fluide et performante. La chaîne de démonstration comprend aujourd’hui deux modules : réseau et infrastructure IT sécurisés pour les opérations, production. Deux modules doivent être ajoutés par la suite pour un contrôle qualité renforcé et le conditionnement. Certaines solutions concernent une étape spécifique et d’autres assurent le fonctionnement global de la ligne de production, de manière transverse.
1. L’importance d’un réseau efficace et continu
L’installation d’un réseau LAN industriel permet de desservir l’ensemble de la ligne de production en fonction des besoins de connectivité IP et Ethernet liés aux contraintes industrielles. Ce système local et sécurisé assure une connectivité sans fil Wifi et 5G en continu et assure une cicatrisation en quelques dizaines de millisecondes en cas de panne.
Sur ce réseau viennent s’ajouter des solutions de cybersécurité qui renforcent la sécurité complète de l’usine. Avec la mini usine, l’objectif est de démontrer les conséquences d’une attaque informatique sur les composants industriels d’une chaîne de production et de proposer des contre-mesures adaptées.
Une solution de supervision industrielle intervient aussi de manière transverse aux modules : le fonctionnement de l’ensemble de la ligne de production est contrôlé en continu, avec le paramétrage de seuils et d’alertes en cas d’anomalie dans le système. Cela permet d'anticiper les pannes potentielles, d’éviter les temps d'arrêt non planifiés des machines et de réduire les couts de maintenance.
2. La production : une multitude d’opportunités d’optimisation
Au niveau de la production, l’optimisation se fait en partie grâce à une solution de condition monitoring. Des capteurs (ou autres technologies IoT) mesurent différents indicateurs faisant partie de l’environnement de la production, comme le temps de fabrication d’une pièce, le taux d’humidité ou la quantité d’énergie consommée. L’analyse de ces données renforce la connaissance des machines, ce qui permet d’optimiser leur utilisation. En cas d'anomalie — par rapport aux chiffres de référence qui garantissent une production sans faille — les alertes permettent aux opérateurs de l'usine de réagir rapidement. Ils peuvent mieux identifier les problèmes et effectuer des opérations de maintenance au bon moment et avec les bonnes ressources, réduisant ainsi les coûts de maintenance associés.
Le condition monitoring contribue également à l'amélioration de la performance ESG, grâce aux mêmes types d'alertes sur les éléments comme la consommation d’énergie des lignes de production ou leur empreinte carbone.
En fin de production, un premier contrôle qualité peut être effectué. C’est le cas sur la mini usine grâce à une caméra thermique qui repère les points chauds de l’opercule d’une capsule de café et vérifie ainsi qu’elle est correctement fermée.
3. La visualisation
Une fois les données collectées, une passerelle (aussi appelée Gateway) permet de les agréger et de les transmettre entre des équipements IT et des équipements OT avant qu’elles ne soient analysées et présentées de manière claire avec des vues adaptées. Ces indicateurs en temps réel ainsi mis en avant facilitent la prise de décision et le déclenchement des actions nécessaires au maintien d’un système fonctionnel et fluide.
En pratique et de manière simplifiée, cette infrastructure met en lien des données avec un réseau local sécurisé permettant de contrôler sa ligne de production en temps réel, d’agir plus rapidement en cas de panne ou de danger et même d’automatiser certaines tâches. L’infrastructure est flexible et scalable : elle peut être mise en place sur une partie de l’activité avant d’être utilisée progressivement plus largement, en fonction des besoins.
Orange Business Operational Xperience Factory : problématique terrain et solution tangible
Cette mini usine est aussi un moyen de démontrer l’expertise et la connaissance terrain d’Orange Business associées à son expertise réseau et Infrastructure IT.
« Les problématiques adressées sont celles rencontrées au quotidien par les équipes opérationnelles et les fonctions support comme l’IT, dont les enjeux sont précisément compris. Cette approche pragmatique sensibilise aussi plus directement la direction ou les personnes décisionnaires en leur montrant très concrètement ce à quoi ils peuvent aboutir en matière d’industrie connectée sur une infrastructure réseau et IT mutualisée intégrant les contraintes de l’OT ».

explique Emmanuel Routier, VP Expérience Opérationnelle chez Orange Business.
Cette démonstration met ainsi en évidence plusieurs grands bénéfices rendus possibles par cette association entre l’IT (technologies de l’information) et l’OT (technologies opérationnelles).
- Une réduction drastique des temps d'arrêt non planifiés des machines, et une anticipation des pannes potentielles ou des besoins de maintenance en moyenne deux jours à l’avance. Ce point est essentiel puisque ¹80 % des industries manufacturières ont fait face à des interruptions de production non programmées au cours des trois dernières années.
- Une amélioration de 15 à 20 % du TRS (taux d’utilisation des machines) selon le type d’industrie manufacturière ou de process.
- ²Une réduction d'environ 20 % des coûts de maintenance, ce qui représente une économie conséquente puisque l’on estime qu’une panne en production représente au moins € 157K de pertes en une heure.
- Une amélioration de la sécurité des opérateurs.
- De manière plus indirecte, une augmentation de la satisfaction client, grâce notamment aux contrôles qualité permettant de réduire le nombre de produits défectueux et à des délais de livraison qui peuvent être raccourcis.
- Une cybersécurité renforcée et en conformité avec la réglementation.
- Une homogénéisation de l’infrastructure réseau et IT pour l’OT sur différents sites opérationnels géographiquement distants.
L’usine du futur évolue, en grande partie grâce aux solutions décrites ici. Les systèmes de production se transforment et deviennent plus performants, ce qui réduit notablement les coûts d’exploitation et augmente l’agilité ainsi que la profitabilité de l’usine. Dans cette transformation, Orange Business vous accompagne de A à Z sur tous les aspects du projet : conseil, intégration, cybersécurité, stockage et traitement des données et connectivité.
« La clé du passage à une industrie 4.0, c’est de mettre en place un rapprochement entre l’OT et l’IT, qui sont encore trop souvent dissociés ».

conclut Sébastien Dudreuilh, Responsable Smart Industries France chez Orange Business.
¹ ² Source : Gartner, GE Digital, WEF, Senseye, “The True Cost Of Downtime, 2021
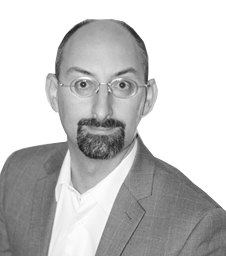
Sébastien Dudreuilh est expert en smart industries chez Orange Business. Il accompagne les industriels dans la digitalisation de leurs processus et élabore avec eux des solutions sur-mesure : convergence IT/OT, cyber protection des moyens de production, exploitation des données des usines, réseaux multiservices, équipements des agents.