La maintenance industrielle : un enjeu capital
La bonne santé de l’outil de production est depuis toujours un enjeu déterminant de la réussite industrielle. Les coûts associés à la défaillance ou au remplacement des équipements sont souvent sans commune mesure avec l’impact que ceux-ci peuvent avoir sur la chaine de valeur.
A titre d’illustration, le remplacement d’un câble électrique défaillant sur un Boeing ne coûte que quelques milliers de dollars, alors que l’immobilisation de ce même appareil peut représenter jusqu’à 150.000 dollars par heure pour la compagnie qui l’exploite.
Inspection de l’outil industriel ou quand l’équation devient inextricable
Le niveau d’exigence pour les entreprises industrielles a fortement augmenté, et désormais de plus en plus souvent les dirigeants en sont responsables pénalement :
- responsabilités à la fois écologique et sociétale
- engagements de plus en plus forts (0 accident, qualité 0 défaut)
- prise de conscience et prise en compte de la pénibilité du travail
D’une part, le recours à des personnels temporaires peu formés pour assumer les pics de production ou comme variable d’ajustement pendant les congés accroit les risques liés à la méconnaissance des consignes.
D’autre part, les opérateurs chargés des inspections maintenance pour l’outil de production sont sujets à des limitations intrinsèques :
- le temps de travail limité (interventions en urgence au détriment des inspections de routine)
- l’impossibilité de surveiller en continu (par exemple les vibrations de pompe ou la fluidité d’ouverture d’une porte de hangar)
- l’accessibilité physique (lieux parfois inaccessibles pour un humain, typiquement une cheminée)
- l’absence de partage de l’information (par exemple, l’inspection maintenance pompe ne partage pas forcément ses observations avec le responsable qualité de l’air)
Ainsi, les opérateurs doivent de plus être formés sur des sujets de plus en plus pointus et variés tant l’outil de production se complexifie.
En conséquence : les moyens humains et financiers nécessaires pour assurer le niveau d’exigence théoriquement attendu devraient croitre exponentiellement.
L’IoT : la solution d’avenir
L’IoT offre la possibilité d’améliorer la maintenance curative et surtout d’aller beaucoup plus loin en matière de maintenance prédictive que le traditionnel M2M (Machine-to-Machine). De la même manière, l’IoT permet d’automatiser et de rendre intelligent l’inspection de l’outil.
Grâce à de nouveaux capteurs et de nouveaux réseaux de type LPWAN (voir schéma ci-dessous), l’IoT permet de surveiller beaucoup plus d’équipements et de paramètres que par le passé :
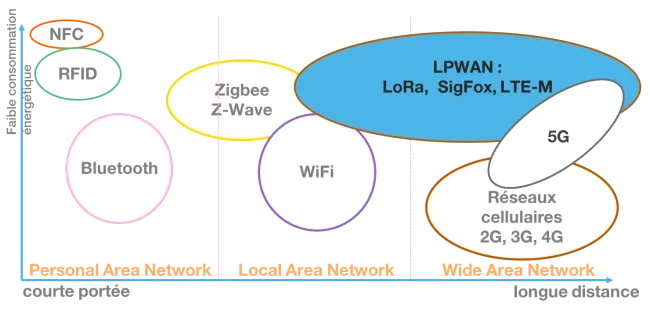
L’IoT permet par exemple de contrôler des équipements dans des milieux industriels très peu accessibles comme des cuves, et ce grâce à des capteurs émergés qui sont dotés de durées de vie pouvant aller jusqu’à 10 ans.
La conjonction de l’IoT et des technologies du traitement des données dites « Big Data » décuple les bénéfices à attendre :
- En collectant de manière continue les données issues de leurs équipements et en les associant à d’autres données externes, les industriels vont pouvoir mieux prévoir et anticiper la maintenance de ceux-ci, et donc ainsi réduire leurs coûts de maintenance, augmenter leur rentabilité et planifier leurs investissements par rapport aux données réelles et tangibles.
- Autre exemple : des capteurs placés sur les turbines des éoliennes transmettent en continu des informations sur la performance du système, qui associées à des données externes de type météorologiques ou historiques permettent d’optimiser les périodes de maintenance de celles-ci, et par là même d’accroitre leurs disponibilités.
Comment améliorer sa maintenance industrielle avec l’IoT ?
La réalisation d’un projet IoT pour optimiser sa maintenance prédictive demeure complexe car elle implique des choix techniques dans des domaines très différents et nécessite l’association de nombreuses expertises et la coordination de multiples acteurs : utilisateurs, constructeurs d’équipements, experts en connectivité ou en Big Data.
La première étape passe donc par une analyse élargie de l’écosystème industriel, afin de déterminer les axes de progrès prioritaires, ainsi que la contribution et les bénéfices que l’IoT pourra y apporter. Ensuite, il sera nécessaire dans un deuxième temps de se familiariser avec son adoption par la mise en œuvre d’une expérimentation (ou POC).
La maintenance industrielle est un domaine d’application privilégié de l’IOT, mais ce n’est pas le seul : la qualité, la logistique, la traçabilité, l’efficience énergétique peuvent aussi s’améliorer et apporter des bénéfices substantiels. Charge aux industriels de prioriser leurs projets et leurs investissements en connaissance de cause.
Pour aller plus loin
[Infographie] Industrie 4.0 : vers une convergence des technologies
Maintenance prédictive : la donnée au service de l'industrie
IoT et maintenance prédictive : bienvenue dans l’industrie 4.0
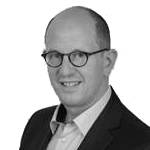
Étienne est Senior Manager chez Orange Consulting, la branche conseil d'Orange Business dédiée à l'accompagnement des clients dans leur transformation numérique. Fort de plus de 15 ans d'expérience en conseil sur l'utilisation des technologies, Étienne s'est concentré sur le secteur de l’industrie, notamment les lignes de production. En tant que spécialiste de l'industrie numérique et de l'intelligence des données, il a contribué à positionner Orange Business auprès des clients industriels grâce à un marketing stratégique et à un accompagnement dans leur parcours vers l'industrie intelligente. Il a soutenu avec succès des multinationales et des PME dans la conception d'infrastructures IT pour l'OT, la mise en œuvre de la convergence IT/OT et le développement de produits intelligents.