The need to transform traditional mining operations is clear. Extraction companies have had to work harder to find fewer valuable resources than previously, and they have had to do it with less-skilled and experienced workers. Companies have invested in digital tools and systems to transform ways of working and overcome these challenges. The World Economic Forum has forecast that $425 billion of value will be added to the mining industry through digitalization between 2017 and 2025.
Research by Berg Insight found the total number of connected mining devices and equipment was just under 0.6 million items worldwide in 2018, but by 2023, it will reach around 1.2 million. Mordor Intelligence estimates that the smart mining market will triple by 2025, with 25% of mines having deployed autonomous operations by then. But where specifically will technology bring value and transformation to mining operations, and how do companies drive returns on investments (ROI)?
Enabling specific, targeted use cases
The mining industry has been using technology-powered solutions for many years. Typically, they are used to make sites safer and more secure for human workers or for automating tasks and activities to drive cost efficiencies. Connected mines take that approach forward. By using a combination of information, data, autonomous machines and state-of-the-art connectivity, mining companies can drive greater productivity, improved safety and reduced operational costs and achieve concrete ROI.
Deploying smart mining technologies successfully requires a strategic approach. They need to be targeted to specific use cases. Examples of this include using autonomous vehicles for hauling ore and resources on mine sites and for making life safer for human workers, or real-time monitoring of machinery and data analytics to make sites safer. Others include remote-controlled drilling equipment, geofencing and sensors on tailings dams. All these use cases will help mining companies operate safer, more efficient and more productive sites.
5G networks will drive transformation
Private cellular networks can provide the robust, reliable connectivity that smart mines need. It can support deploying IoT sensors around a site, implementing automation in unmanned trucks or remote monitoring. Connected mines must also be capable of handling large amounts of data generated by those autonomous vehicles, connected systems and networked devices.
The technologies needed to transform a mine into a smart mine also include things like live, real-time video feeds, which need sufficient bandwidth and reliable connectivity to function. Furthermore, mine sites have always needed critical voice and data communications around them to enable real-time contact, particularly important in emergencies. 5G can support all of this.
Think of a mine site as an isolated campus that needs high-speed connectivity, low latency and robust performance in a high-device-density environment. Mining companies typically need to be able to send high resolution images around a site, for which they need low latency and high uplink speeds – again, one of 5G’s strengths. Remote drilling is also better enabled by a 5G private cellular network, as it is able to operate in both licensed and unlicensed spectrum.
According to research by Ericsson and Arthur D. Little, when deployed concurrently, autonomous vehicles, real-time site monitoring and remote-controlled drilling rigs deliver improved efficiency, productivity and safety and a combined ROI of 207% over ten years in surface operations. In underground mining, the ROI equates to 256%. Digital is driving real change in mining.
Not forgetting the ethical imperatives
Connected mines are also safer, more environmentally-friendly operations. Mining is by nature a hazardous job, and according to the U.S. Bureau of Labor Statistics, it is among the ten most dangerous professions. Connectivity and digital solutions building smart mines can help make sites safer in general: Accenture and The World Economic Forum found that as many as 1,000 deaths and 44,000 injuries could be prevented in the coming ten years.
Making mining operations more sustainable and ethically sound is something else connected mines can contribute to. Digital tools have helped make the mining industry safer in general in recent years, but there is always more to do. Connected workers, 3D-modeling, digital twins, environmental modeling and autonomous vehicles all give site operators access to enhanced monitoring, helping identify potential trouble spots before they occur.
Automated operations also mean more efficient fuel usage and lower CO2 emissions, adding to a company’s ethical and social governance (ESG) rating and making them a more acceptable neighbor to nearby towns or cities. In time, it is hoped that tools like AI and ML will add to the connected mine mix and improve operational efficiency through predictive distribution of minerals and by-products.
The importance of partnerships
Mining companies can’t deliver connected mine sites by themselves, though: they need the right blend of expert providers to get there. The Ericsson and Arthur D. Little report cited additional smart mine partners in Komatsu and Epiroc, who provide autonomous trucks and drill rigs and excavation tools, respectively.
Orange understands this need and has recently worked on initiatives that underline our commitment to projects like connected mines. In Asia Pacific, Orange has a strategic alliance with GHD, a mining industry specialist. Our IA Alliance helps mining companies avoid tailings dam accidents by combining IoT sensor technology, data analytics and extensive mining expertise and helps make sites safer and more environmentally friendly. This wouldn’t be possible without an ecosystem of partners in place. Another Orange project, Port of Antwerp, operates a 5G private cellular network to make the port site more efficient, safer and more productive, again leveraging the expertise of an ecosystem of partners and underpinned by a state-of-the-art network.
Digital technologies like 5G cellular networks supporting cutting edge tools, deployed by the right ecosystems of partners, will be essential to driving the mining industry forward. Connected mines will be the next step on that journey. Mining giant BHP was recently ranked as the most valuable company in the FTSE 100 for the first time, demonstrating that mining companies can bounce back post-pandemic, and thrive. Connected mines will ensure they can do it quickly and effectively and take operations to the next level.
Uncertainty and impending erosion of demand is pushing change throughout the natural resources industry. To remain successful in this environment, your priority should be strengthening operational foundations with data, analytics and connectivity to drive cost improvements and increase productivity gains. Find out how to leverage real-time data to improve operations and increase RoI.
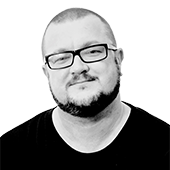
I’ve been writing about technology for around 15 years and today focus mainly on all things telecoms - next generation networks, mobile, cloud computing and plenty more. For Futurity Media I am based in the Asia-Pacific region and keep a close eye on all things tech happening in that exciting part of the world.