Operational experience addresses the digital tools, processes and infrastructure that improve performance, productivity and worker motivation. It can also reduce costs and ultimately improve quality and customer satisfaction.
How mature is your factory floor's operational experience and uptake of Industry 4.0, and are you ready to take it to the next level?
Bringing data analytics to the factory floor
Accurate data is fundamental to Industry 4.0, but its collection on the factory floor can be difficult, inconsistent and manually intensive. This can lead to poor insights. In addition, older machines may not have data collection capabilities. This may require gateways or sensors to pull in or create new data. In addition, there may be legal hoops to jump through. Some vendors, for example, may have contracts that deny enterprises accessing some internal data unless done via an API to the cloud.
According to IDC, becoming a data-driven enterprise requires an honest assessment of the current state and a willingness to adopt change to improve operational performance. To manage the data produced on the factory floor, an actionable strategy for what to do with the captured data and where its value lies is essential. This strategy should consider all production facilities and interrelated processes, not just individual machines.
Identifying strengths, inefficiencies and opportunities
Every factory has its own pain points to consider. The best place to start is with an initial operational experience maturity assessment to understand the specifics of the factory floor and implement the right solutions, training and safety mechanisms. This can include consultation with workers who can provide a full picture of the inner workings of the processes they are responsible for, areas they are worried about, and where improvements can be made.
By investing in a maturity assessment, enterprises can pinpoint issues and where their investment is best targeted to achieve business outcomes. It allows them to avoid costly disruptions, ramp up the adoption of digital technologies and maximize productivity, while keeping workers happy and motivated.
Continuous improvement in Industry 4.0
Cultural and operational transformation, including organizational restructuring and technological integration, are also an important part of operational experience. Cultural transformation is vital because it lays the foundation for successful adoption and sustainability of operational improvements.
This continuous improvement mindset can sometimes cause resistance among workers worried about automation, for example. This is especially the case if changes disrupt traditional workflows or require significant adjustments in worker behavior.
In terms of digital industry, workers need to understand that technology is not there to replace their roles but to open up opportunities. While insights can optimize processes, human judgment is still critical for handling unexpected events or complex problem-solving on the factory floor.
In fact, operational experience frees up workers from mundane and repetitive tasks to handle the surprising and accidental, allowing them to focus on problem-solving and process improvement. Change management and training can explain how their roles will become more engaging as a result, reducing worker churn.
This is critical to the bottom line. McKinsey estimates that each frontline employee departing can cost an enterprise $52,000 annually in recruiting, training, onboarding and productivity losses, which can add up to a significant amount across production lines.
Operational experience improvements in action
We have helped several manufacturers improve their Industry 4.0 processes on the factory floor.
One industrial customer found it difficult to locate tools in its warehouse to maintain big machines. Workers found it frustrating, wasting unnecessary time. To solve this issue, we worked with the shop floor to understand the industrial processes and provided them with a real-time inventory and location system. An interactive map highlights the location of all the tools tagged with a tracking sensor. The system has enabled the shop-floor team to see the tools' whereabouts accurately and better manage resources.
Consulting with another customer, we talked to the shop-floor team and found it challenging to manage production lines. Daily planning was done on paper and included the entire manufacturing process down to packaging and dispatch. This excess information overload was confusing staff and causing production issues.
Orange Business developed a visual management system that splits the production lines into screens, similar to the departure board at an airport. The real-time system eliminates excessive data, simplifies production line visibility and makes it much easier to manage production line processes.
Production line perspective
Implementing the right digital industry strategy on the factory floor really is a win-win situation. By strategically evaluating how well processes, machines and personnel perform in a production line environment, the shop floor can maximize the value of OT data linked to an IT environment for smart decision-making.
Running an initial maturity assessment of the operational experience, however, is crucial to ensuring the readiness and capabilities of the enterprise and its workers to adapt to new processes and technologies —whether you are starting out or looking to see where you sit on the development curve.
Without the right foundational elements in place, such as data availability and work skills in production facilities, enterprises will not be able to take advantage of the benefits operational experience offers, leaving them frustrated and disappointed.
This is exactly why Orange Business devised an assessment tool that will accelerate your journey toward optimizing your Industry 4.0 strategy. It will enable you to align with industry best practices and build a clear and actionable roadmap for success.
Understanding your Industry 4.0 maturity is pivotal in providing insights into how effectively you manage operations on the shop floor and across the entire plant. To find out how you score, take our short, free-of-charge introductory assessment.
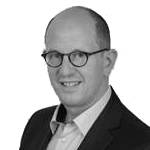
Étienne is a Senior Manager at Orange Consulting, the consulting arm of Orange Business dedicated to supporting clients in their digital transformation. After 15+ years of advisory work on technology use, Étienne focused on the industrial sector, notably the production floor. As a digital industry and data intelligence specialist, Étienne has contributed to positioning Orange Business to industrial clients with strategic marketing and accompanying several industrial clients in their journey toward smart industry. He has successfully supported multinationals and SMEs in designing IT infrastructures for OT, implementing IT/OT convergence and smart products.