Internet of Things gaining traction
The Internet of Things (IoT) has the potential to dramatically transform Australia's mining industry. Around a year ago, research company Vanson Bourne surveyed 100 large mining companies for its "The Future of IoT in Enterprise – 2017" report, and found that 40 percent of mining companies around the world have plans in place to deploy IoT solutions within the next 18 months, so effectively by early 2019.
Worker health and safety at mine sites appears to be the area where mining companies are expecting to feel the most benefits: 44 percent of mining companies foresee IoT solutions helping improve the health and safety of their employees.
What else is driving IoT adoption?
Further drivers for IoT adoption in the mining sector include monitoring environmental changes on mine sites and improving cost effectiveness, with 47 percent and 44 percent respectively telling Vanson Bourne that these were their primary objectives for designing and implementing an IoT strategy.
Why is this happening?
In Australia, where mining is a major, traditional industry but also one that has sites in very remote locations, IoT technologies can make things markedly safer and more efficient for companies and their workers. Mines are highly specialized and hazardous environments that need to focus on employee safety as well as productivity and efficiency, and IoT technologies have changed the game. Automation is changing the way mining companies send extraction machinery and hauling vehicles into dangerous mines, taking the human worker out of harm's way.
Further, IoT-connected wearable technologies and sensors worn by workers on their site clothing can help improve the site by monitoring conditions and gathering data that is subsequently analyzed and used to pre-emptively eliminate potential safety threats.
All this takes place in real time, too, meaning IoT tools can adjust to environmental conditions in real time and react to any potential hazards on the mine without the need for human intervention. The benefits to mining companies can be huge.
Robots on the rise
Rio Tinto, one of the world’s biggest mining companies, has recently introduced us to the "world’s largest robot," a fully autonomous train that on its maiden journey transported 28,000 tonnes of iron ore from the company’s Tom Price mine site to the port at Cape Lambert. The train was being monitored remotely by operators in Rio Tinto’s Perth operations center 1,500 kilometers away.
Connecting up these advances
But all these digital tools need connectivity, and connectivity has always been a challenge for remote, geographically disparate sites and locations like those of the mining industry. And potentially the best connectivity option for mining companies could be LoRaWAN (Long Range Wide Area Network).
Historically, one of the chief concerns of providing connectivity to remote mining sites was cost – cellular and satellite connections can run expensive. This is one of the plus points of LoRaWAN, since it has a unique penetration capability and is relatively quick and easy to install: LoRaWAN can be deployed on a building or a tower and can connect to sensors over 15 kilometers away or to mining sensors and wearables deep underground.
Environmental impact a big factor
IoT tools can also reduce mining operations' impact on the environment quite dramatically, and mining companies have recognized this: according to the Inmarsat report "The Future of IoT in Enterprise – 2017," 47 percent of mining companies cite monitoring environmental changes as their top priority for IoT deployments, with a further 53 percent saying environmental monitoring is the most exciting IoT innovation in their opinion.
Progressive companies like Rio Tinto have already established integrated remote operational centers that can monitor their mining operations via IoT technologies, so monitoring their environmental impact is the next step. IoT solutions let them gather data more quickly and accurately, which they can then analyze and use to react more quickly to any potential issues, giving them more control over their operations, improved impact assessments and, ultimately, less environmental damage than previously.
Predictive equals pre-emptive
Furthermore, the data gathered by IoT sensors on a remote mine site can be used to reduce operating expenditure, or OPEX, too. In 2014, Mining Global estimated that maintenance costs accounted for between 30 and 50 percent of a mine’s total operating expenses, a significant amount.
IoT-enabled sensors on vehicles and machinery can help mining companies use predictive analytics to make real-time decisions that can hugely impact throughput, recovery, equipment reliability and availability. Similarly, early warning notifications give mining companies longer lead times to plan and carry out necessary maintenance – and this monitoring, thanks to IoT tools, all takes place in real time.
Mining major benefits from digital
The IoT, digital tools and the mining industry seem like a perfect marriage. Digital solutions can enable mining companies to be more productive and more profitable, while at the same time help them reduce the danger faced by human workers.
Mining companies appear to be taking note and investing in smart digital tools to enhance operations. The smart mining market is forecast for major growth in coming years, according to a report from Transparency Market Research: in 2014, the global smart mining market was valued at $US5.98 billion but is predicted to grow to $US22.59 billion by 2024, at a CAGR of around 15 percent per year. Australia’s mining companies will look to be at the forefront of that investment and leverage the big benefits that digital can bring to their operations.
In future blog articles, I will take a look at other elements of smart technologies in Australia and what we can look forward to. In the meantime, to read further about how Orange is enabling the cities of the future with digital technology, please visit: Supporting the digital transformation of cities and territories.
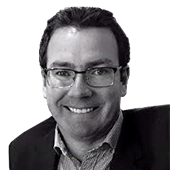