Detect incidents as quickly as possible to limit risks
The IT department’s work is time critical. It must identify the cause of an incident as quickly as possible, within a complex architecture with multiple interconnected services. There are many different types of risks to be mitigated. Let's look at a few examples:
- A loss of connectivity to equipment protecting a machine operator can put that worker in danger
- A production shutdown at an automobile factory after a cyberattack can cost the company one million dollars per day
- A database problem in a cosmetics plant can stop its daily production of millions of units, with the ensuing commercial impact
- In a petrochemical or heavy industry plant, a production restart will be even more expensive. The time to restart the lines and reheat the furnaces, perishable raw material stock will be lost, and additional quality controls will be required
IT departments in manufacturing are always seeking tools to anticipate, respond more quickly to and reduce internal risks (such as unplanned shutdowns or the development of shadow IT1) and external threats (cyberattacks, misuse by a subcontractor, etc.).
1 Use of information systems, devices, software and applications without the explicit approval of the IT department
Tackling the silo-based organization of IT services
In the industry, monitoring the information system performance relies strongly on a siloed structure. It is usual to separate information technology (IT) in charge of desktop tools, CRM or ERP systems from operational technology (OT) dedicated to production tools.
The IT department is increasingly called upon to deal with industrial issues in their entirety. While IT and OT have two very different cultures, many production applications now feed information to cloud platforms to which IT teams provide accessibility. Collaboration between IT and OT is particularly crucial for cybersecurity in order to deploy a common protection strategy.
However, the overall supervision of IT services performance remains difficult. Each plant has its own specificities, and the IT department must adapt to them. This is particularly true in the case of an industrial site buy-out: it is necessary to manage applications with their own monitoring and maintenance system. One of my customers recently mapped all the applications and servers installed at their plants and assessed their level of risk to prioritize their supervision.
Cross-functional supervision of the information system, without adding a new application layer
How can we have this cross-functional supervision of different IT-OT systems? This is what is offered by Service Manage - Watch, which interfaces with multiple monitoring tools already in place and centralizes their data in a single supervision tool. Advances in artificial intelligence allow Service Manage - Watch to correlate application data to better understand the various sources of holdups or blockages in the process or even anticipate potential incidents. This overview serves businesses and helps anticipate the obsolescence of some IT system elements, like outdated operating system licenses that can cause a machine to malfunction.
Another benefit of Service Manage - Watch: the IT department can rely on our experts to analyze its supervision data. It can also benefit from the experience of other companies with similar problems, obviously with the required confidentiality and data anonymization.
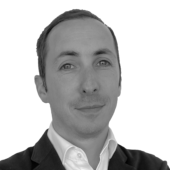
As an Industry Business Developer at Orange Business, I provide my clients with the best technologies and innovations from the world of IT and OT. Together, we seek to improve the safety, quality and productivity of their industrial activities by using digital technology for the service of people.