According to the U.S. Occupational Safety and Health Administration (OSHA), the oil and gas industry has a fatality rate of seven times that of the total of all other industries.
This sobering figure underlines that working in the field can be very dangerous if procedures are left unchecked. The field is full of heavy machinery in motion, rigs and masts are high, restricted chemicals are stored and byproducts are highly flammable, against the backdrop of a job that can be extremely fatiguing.
Workers need to be trained to understand potential vehicular accidents, being struck by equipment, explosions, fires and electrical hazards, falls and risks related to confined spaces and chemical exposure. Extreme work environments, often in remote locations, run the risk of worker health hazards including hearing loss, frostbite, burns, respiratory issues, and acute physical fatigue and injury caused by moving heavy loads. Workers also need to be able to cope with so called “fly in, fly out” operations, which involve journeys to remote locations for set periods of time, where shifts can be long.
Another factor is that Health, Safety and Environment (HSE) is a dynamic area. For example, there’s been a recent increase in hydraulic fracturing operations, and this has led to concerns about potential injury to workers from airborne silica used in the fracturing process.
Every day in the field can present risks to employees who are unaware of or disrespect safety procedures and to managers who want only the best for their teams but can’t be everywhere at once.
In the U.S. at least, incidents are on the wane, even though oil production has grown significantly in the past 15 years, doubling the workforce. A recent Centers for Disease Control and Prevention (CDC) study, concludes that this is because of “rapid development and adoption of technological advancements that have reduced workers exposure to dangerous situations.”
The industry is at the beginning of a technological revolution that puts added eyes and ears into the field, triggers early warning systems and can dispatch appropriate medical assistance immediately, with 100 percent accuracy.
Employee safety
Today’s employee safety recommendations are no longer just hard rules, although these still form the foundation of training. Companies are exploring moving beyond the basic observance and practice of safety to real-time safety monitoring and prevention. This is happening both in real time, which reports on operations as-they-happen, and with predictive assessments, which forecast likely outcomes of specific situations and warn of potential risks before employees even begin their shifts.
The key to these is an innovative combination of technologies including IoT and other devices, GPS positioning systems, LoRA signal transmission (which allows penetration of remote or deep locations), Wi-Fi and cellular networks, and behind the scenes, analysis of Big Data and data lake information.
For example, four out of every ten deaths on the job are motor vehicle crashes, making them the leading cause of fatalities in the sector. Most of these incidences are triggered by tiredness, distracted attention or traveling unconventional off-road routes, but vehicle monitors can measure direction, excessive acceleration, deceleration or lane skipping and alert the driver to pull over. Over time, analysis of historical vehicle data provides insight into certain areas of the transport chain that present heightened risks, and enables planning accordingly.
Minimizing on-site risks
Fortunately, there is very rarely an on-site fatality. Three out of every five of these, however, are the result of incidents involving employees coming into contact with moving vehicles or equipment, equipment in motion, falling equipment and high-pressure lines.
Further hazards are associated with confined spaces, include ignition of flammable vapors or gases, or outside of the space, exposure to hazardous chemicals and gas leaks.
But very soon, employees will themselves become beacons that alert to hazards by wearing devices that let managers know where they are and offer a constant view into their work practices, even in remote locations.
This information can be transferred to visual mapping that shows everyone’s position and corresponding proximity to dangerous areas, such as those that have restricted access, or which have just become a hazard following an incident.
As incidents evolve, so does the map, to become a real-time analysis of workers within field operations. Command-and-control decisions about containing areas can more easily be made, and medical assistance can be dispatched to the location with the required skills.
Workers can also carry SOS buttons on their belts that alert to their situations and confirm their locations and status. Increasingly, drones will provide a view of what’s actually happening and add an extra set of eyes and ears to decision making.
Connected CCTV is developing into a powerful safety tool, and soon Artificial Intelligence (AI) will be able to analyze video feeds and forewarn of potential dangers by collecting the visual cues that have led to previous incidents – and then predicting the next one.
Employee welfare
Alongside keeping employees safe, organizations need also to be involved in welfare, ensuring employees are happy and healthy.
Mental health is an issue in the oil and gas industry, where workers are often away for long periods of time. Poor mental health can manifest itself in various conditions and disorders. Stable connectivity can help workers stay in contact with friends and family when they are away, helping relieve the feeling of isolation. Phone apps have the potential to cut down mental health related incidents, providing advice and resources. Using the same connectivity, telemedicine can be administered in remote locations to provide constant care onsite, not just when they’re at home.
In addition, companies may soon help workers stay fit with new personal devices and ensure that they’re healthy when they’re at work. Bracelets that monitor blood pressure, blood/oxygen saturation level and pulse, show data that’s helping companies proactively avoid issues such as physical fatigue, illness and tiredness.
Another new technology will see the implementation of augmented reality through devices and smart glasses. This enables workers to visualize the job ahead of them, “see” technical detail inside equipment, streamline tasks to meet best-practice guidelines, and help with troubleshooting guidance in unfamiliar situations.
As the industry expands, managing the workforce will become more challenging, and a good health and safety record coupled with a good welfare program can go some way to persuading applicants to apply for new oil and gas jobs.
Download our white paper Compelling opportunities in oil and gas present new challenges to find out more about strategies for keeping employees safe at work.
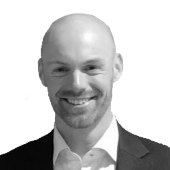
Olivier Vicaire has been a business consultant for more than 10 years in Paris and London and is a specialist in digital transformation. With a telecom engineering degree and a Masters in marketing, he manages innovation, digital workspace strategy and user adoption programs to drive digital transformation for the employees of Orange Business customers.