The oil and gas industry explores, produces, transports and processes billions of tons of crude oil and cubic meters of natural gas and their derivatives each year. Aside from the well-documented but extremely rare oil spills of the last couple of decades, the industry has a reasonable reputation for management of environmental risk. But pioneering techniques to recover resources from shale gas deposits, coal seams and tight sandstone, for example, pose new environmental challenges.
There are a multitude of environmental regulations that the oil and gas industry must comply with. Firms are worried about the impact that an infringement might have. It could affect their reputations and force them to face legal and financial penalties.
It’s a complex picture, and the solution lies in monitoring and reacting to the entire operational lifecycle as if it were a living organism.
The role of IoT, sensors and devices across the operation
IoT delivers this holistic picture by helping generate granular operational data. This allows companies to minimize their risks to the environment, and even predict and prevent problems before they happen. Alongside monitoring of infrastructure, systems and logistics comes a real-time feed of information that leads to shorter time to resolution and therefore less risk of damage to the environment.
IoT provides three environmental insights: baseline monitoring that establishes pre-existing environmental conditions; operational monitoring, during construction, recovery and production activities to identify any deviation from the baseline; post-closure monitoring after production completion, well decommissioning and site restoration, to check for potential impacts.
Coupled with the rapid analysis of information in data lakes, a highly detailed snapshot of the entire operation is available at any given time. If there is an incident, it’s located and mitigated much more quickly than normal by workers who are in proximity.
A real-life example of leakage and mitigation using IoT
In today’s lengthy, remote and diverse pipelines, an average leak detection time of one minute for every 10m of pipe is not timely enough when pipelines stretch thousands of kilometers, yet regulations are tightening.
Using flow/pressure and pipe vibration tools coupled with IoT sensors, detection times are reduced, even when there’s no electric power to these locations. Issues are spotted at operational centers rapidly rather than a much longer process of manual discovery and driving back to the central facility.
Drones are now being used by some of the world’s largest oil and gas companies to augment leak spotting and to provide visual evidence of spillage so remote maintenance workers can be prepared with the right toolsets before they arrive. Crews with wearables can be mobilized and instructed on the issue circumstances beforehand, and to save further time, only crews with the closest proximity are involved.
Total lifecycle management
Exploration and extraction of existing and new, more remote resources demands an IT infrastructure that supports effective operations. Although IoT devices form the basis of this, new technologies in the network, databases, data center, analytics tools, tracking and reporting dashboards form the basis for the framework that integrates an IT and communications nervous system.
Unconventional gas exploration and extraction has the biggest impact in up-stream operations where hydraulic fracking carries pollution risks. Treatment systems for injection water and wastewater, hazardous waste and byproduct chemical spread damage can be detected earlier than ever, even when monitoring an operation running at huge volumes.
In the mid-stream, one exciting future development will be 3D printing, which can help expedite fixing leaks in transport pipelines. Today, workers arrive at a breach and use IoT devices to capture the issue and order spare parts – which is far more effective than manual inspection, which takes more time. In the future, fixing leaks or mechanical issues will minimally impact the environment because if a spare part is not available, it can be rapidly printed and applied in the field.
Down-stream, approximately 75% of gas produced is flared every year. Excessive flaring and wastewater discharge present the biggest problems and, if there’s a mishap, affect the natural ecosystem in a substantial way. Although today, these operations are already watched closely, IoT monitoring and reporting can offer up data that can improve the efficiency of the operation, reducing the amount of waste products released.
In summary, despite the size and steep gradient of environmental care and corporate social responsibility challenges in the age of UGEE, IoT is at the core of corporate strategies to make oil and gas organizations more responsive to environmental risks and become even greener operations. And that’s good for our natural world.
Download our white paper Compelling opportunities in oil and gas present new challenges to find out more about technology solutions for protecting the environment.
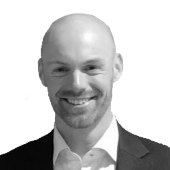
Olivier Vicaire has been a business consultant for more than 10 years in Paris and London and is a specialist in digital transformation. With a telecom engineering degree and a Masters in marketing, he manages innovation, digital workspace strategy and user adoption programs to drive digital transformation for the employees of Orange Business customers.