For most businesses, energy consumption has been simply a fact of operating. No matter what industry, every organization requires energy, and while those with heavy consumption will have kept more of an eye on the cost, it was rarely a major cause for concern.
That has now all changed, and in the space of just a few months. All businesses are looking for ways to keep their energy costs under control irrespective of size or sector. For some companies, it can feel like an exercise in futility – they must consume a lot of energy to operate effectively. Even if they can pass some of the cost on to customers, it could be extremely painful in the coming months and years.
From saving energy to cost avoidance
As such, it’s unsurprising that many businesses are looking to manage their costs as effectively as possible. For instance, one energy-heavy manufacturer now employs corporate energy management specialists, and the topic now dominates leadership meetings. They’ve gone from thinking about energy as something they can save to how they can avoid as much cost as possible.
But if you’re a business that must keep specific machinery constantly running, avoiding any cost can be incredibly difficult.
How do you mitigate that impact? It starts with knowing how much energy you consume. Not what the makers of all the machinery and lighting and technology you use say it consumes, but genuinely knowing, in real-time, the exact amount of electricity you are getting through.
The added value of energy consumption data
That can only be done by gathering data from your machinery. It could be the direct power and current consumption of a specific machine or a section of a production line. It could be all of that, but only at certain times of the day or with different variables removed or added.
The point is that by gathering this data over time, businesses can start to see how much power is being consumed and by what machinery. When reviewed against other metrics, this insight can then be used to make informed decisions.
It might be that the heating system for the entire factory is consuming more electricity than previously thought. The manufacturer mentioned earlier realized more than $10,000 in annual savings by reducing the overall temperature in one factory by two degrees.
What’s more, measuring energy consumption doesn’t necessarily have to be confined to informing energy-based decisions. The insights it produces might highlight other areas that need addressing.
For example, energy consumption data from a piece of machinery might indicate that it is not as efficient as it should be, providing evidence that further investigation is needed. If it subsequently turns out that maintenance was required but that this would not have otherwise been obvious until it was too late, the energy consumption data has not only highlighted an inefficiency but potentially averted the need for a costly replacement.
It can also be used to support procurement decisions. Historically, many manufacturers may have chosen to go for equipment with lower capital expenditure that perhaps wasn’t as energy efficient. That has changed. The manufacturer previously discussed is more likely to consider equipment with a significant up-front cost if it is demonstrably more energy efficient. It also requires machinery suppliers to provide accurate kilowatt-hour data up front before it makes any investments in new equipment. It can then combine this information with its existing energy consumption data to see whether any replacements will significantly impact its overall energy use.
Advanced insights with retrofitted technology
Of course, say data to some people, and they immediately start thinking of advanced technologies that require a significant up-front investment. And while those tools are available, the barrier to benefiting from measuring energy consumption is much lower than many would think. That’s because much of the technology involved is readily available and can be retrofitted to existing machinery. Whole production lines do not need to be ripped out and replaced with smart updates; small sensors can be attached and wired into existing interfaces to start gathering data quickly. Thermal imaging cameras can be set up to monitor the insulation properties of machinery and highlight any heat loss.
This doesn’t just have to happen inside a factory, either; the same tools can be used to measure the energy efficiency of entire buildings, providing data that can inform utilization decision making as well.
The point is that data can be gathered easily without significant upheaval. The increased use of cloud and software-as-a-service applications, including advanced analytics, means that the systems needed to store, process and interrogate the data can be deployed as required, rather than with major CAPEX.
A step towards smarter manufacturing
Perhaps the greatest value a manufacturer can derive from its energy consumption data is not energy cost savings. Rather, it is a step on the road to understanding the true, accurate real-time costs of an organization.
For instance, a manufacturer could combine energy consumption data with all the other information it gathers from its operating costs, right down to employee salaries, to understand precisely how much it costs to run a factory at certain times of the day. In doing so, it then starts to understand the margins on products produced during that period. That granularity can then be fed back into decision making that dictates when and at what capacity a factory, or even a production line, should be operating. The organization as a whole is further along in its journey to becoming a smart manufacturer with the agility to rapidly adjust to changing market demands and seize opportunities.
And while that could mean new markets and customers, it could also mean being better placed to react and avoid the impact of rapidly rising energy costs in the future.
Capturing energy consumption data is a critical step for manufacturers wanting to manage their costs and become smarter but doing so can be complex. At Orange, we have extensive experience with the technologies needed to gather and analyze that data. To find out more, get in touch today.
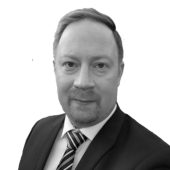
Johan, IIoT & Industry 4.0 Solutions Architect at Orange Business, architects digital solutions for industry, working with manufacturers to do more with less and always investing in creating value as the means of explaining why architecture is important. Outside of work, he enjoys spending time with family, eBiking, skiing, ice skating and learning to play golf.