Using connected sensors inside critical devices means it is possible to monitor production equipment in real time, enabling a new “predictive” approach to maintenance that can cut costs, improve manufacturing capacity and avoid equipment malfunction.
The connected machines will tell us when they need to be repaired before repair is necessary which should reduce wasted maintenance checks while minimizing the risk of asset failure. There are already many examples of these technologies in the wild.
ThyssenKrupp Elevator
ThyssenKrupp Elevator maintains over 1.2 million elevators worldwide. “We wanted to go beyond the industry standard of preventative maintenance to offer predictive and even pre-emptive maintenance, thereby guaranteeing a higher uptime percentage on our elevators,” said Andreas Schierenbeck, CEO, ThyssenKrupp Elevator. To achieve this the company developed a pilot elevator monitoring system that used real-time data to assist.
The aim was to create a predictive monitoring system, in this case built upon Microsoft’s Azure cloud environment and machine learning . The solution collects data from a range of elevator sensors and processes this information to generate rich data insight using predictive analytics. The insights the system creates are made available as maintenance alerts, instructions and recommendations. The impact? The company was able to reduce elevator downtime, improve resource and cost planning, and improve maintenance scheduling.
Ford
Ford has begun limited tests of an algorithm that uses car data in order to predict when a vehicle’s brakes need to be maintained, letting driver’s know with a text message. The system is capable of altering the algorithm in response to specific conditions, such as driving skill, distance or the pressure a driver places on the brake pedal. Similar solutions are being developed elsewhere in the vehicle industry, for example Hadoop developer Hortonworks is collaborating with HARMAN Infotainment to create predictive software for vehicles.
“Combining the capabilities of HARMAN services and Hortonworks, automakers and their suppliers will have access to a scalable platform for, real-time insights, new innovative service creation and predictive analytics-based solutions that can minimize the risk of costly recalls and reduce warranty expenses,” said Sanjay Dhawan, president, HARMAN Services Division.
DTE Energy
Estimates claim US businesses loses an average $15,709 every 30 minutes during a power outage, so there are profound economic consequences to improving the efficiency of power supply. DTE Energy modernized its grid using low-cost software‐defined, inductively powered (battery‐free) connected sensors it put across its power network and used in conjunction with a predictive grid analytics solution. Among other things the system has become able to give advanced notice (up to 15 minutes) of power supply faults before they take place, while as the quantity of historical data accumulates the company is now able to see fresh insights warning of possible disturbance. This technology can also be usefully applied in local scenarios, it was used to help a large North East US utility identify and resolve the cause of flickering lights to several hundred customers. DTE Energy now claims to be running proactive maintenance 80 percent of the time, with just 20 percent reactive. “This all translates into lower costs and high reliability and better service for our customers,” said Edward Nickolite, IT Manager at DTE Energy. In the UK the National Grid is developing similar tools.
Nidec
Press machine manufacturer Nidec recently announced a joint development partnership with IBM in which the partners intend creating big data analysis systems that enable fault detection and predictive maintenance. Nidec attached sensors to its machines, analyzed data collected from those sensors and successfully developed a technology to detect tooling-related and other problems with products based on the data analysis. This should reduce tooling-related downtime, extend their press machines' durability and improve the machine's production rate, well in line with the project’s aim to “detect problems before humans do”, and to “execute measures for such problems even before they occur”. McKinsey & Co say in a recent report “We estimate predictive maintenance could reduce maintenance costs of factory equipment by 10 to 40 percent.”
Healthcare
Predictive connected solutions are proliferating in healthcare, where medical asset tracking can make a life or death difference by saving time when it comes to locating equipment. Today multiple companies (such as Redline PdM) provide predictive maintenance services for key healthcare infrastructure, from fans to chillers, air conditioning to elevator shafts – limiting health institution exposure to unexpected infrastructure problems, enabling them to focus on saving lives.
Smart cities
Examples for smart cities abound. Take the intelligent LED streetlights developed by Blue Yonder and Capgemini which illuminate in response to set criteria. This is combined with functionality to reduce maintenance costs. DynamicMonitors offers SepticSitter, software that monitors a septic tank 24/7, and will send maintenance notifications and alerts to any Internet connected device, allowing corrective action to be taken, before hazardous and costly back-ups or failure occurs.
The implications of predictive maintenance aren’t confined to physical infrastructure – think about smart public transit systems that watch traffic flow in order to predict congestion and take corrective steps to resolve the problem before it becomes one.
These examples illustrate the potential of predictive maintenance, which should introduce new efficiency and also enable enterprises to develop future revenue streams.
“Better predictive maintenance using IoT can reduce equipment downtime by up to 50 percent,” say McKinsey & Co. This could have a potential economic impact worth nearly $630 billion per year in 2025, the analysts claim. Meanwhile, GE and Accenture’s 'Industrial Internet Insights Report' predicts global spending of between $500 billion and $15 trillion on Industrial Internet applications by 2020.
Read more about how Orange Business can deliver the network connectivity and expertise to help you improve enterprise business processes, increase productivity and cut costs with M2M.
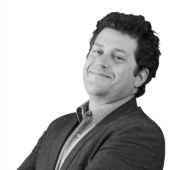
I've been writing about technology for nearly 20 years, including editing industry magazines Connect and Communications International. In 2002 I co-founded Futurity Media with Anthony Plewes. My focus in Futurity Media is in emerging technologies, social media and future gazing. As a graduate of philosophy & science, I have studied futurology & foresight to the post-grad level.