Artificial intelligence (AI) coupled with robotics and the Internet of Things (IoT) will revolutionize how everything in the world is manufactured from cars, ships and planes to clothing, chemicals and computers.
Innovative manufacturers are already using AI as part of “Industry 4.0” for predictive maintenance and automated quality control. This is only just the beginning of a smart journey that will change the factory floor forever.
Previous industrial revolutions have brought us industrialization, mass production and digitization. The next, according to Professor Klaus Schwab, founder and executive chairman of the World Economic Forum, will “fundamentally change the way we live, work and relate to one another”, and be founded on a world of connected devices and smart technologies. AI will play a central role in this cognitive era.
Preparing for change
AI’s road to revolutionizing manufacturing operations management, however, doesn’t come without its challenges. Change management, analytics maturity and skills will need to be addressed first, according to Simon F Jacobson, research VP at research firm Gartner. Jacobson maintains that connecting human thinking and machine analysis in manufacturing operations will require supply chain leaders to concurrently develop new data science and communications skills.
The manufacturing sector has to prepare itself for the concept of fully-networked factories where the entire production process from design, supply chain, production and quality control to distribution are all integrated into an AI solution that can provide real-time actionable insights 24/7.
Manufacturing has always been open to adopting new technologies such as robotics and the race is already on to get ahead of the AI curve. Market research company IDC forecasts that the global spend on cognitive and AI systems will hit $12.5 billion this year, an increase of 59.3% over 2016. Revenues are expected to reach $46 billion by 2020. Manufacturing has been highlighted as one of the strong growth sectors for this period.
Some governments have already been quick off the mark to recognise the importance of smart production in their economic futures. This includes China with its Made In China 2025 program designed to help make the nation a leading manufacturing power. Others include the European Union’s Factories of the Future initiative, which has been developed to adapt manufacturing to what it refers to as a “smart, green and inclusive economy”.
Intelligent automation
AI and advanced automation will provide a “level of accuracy and productivity beyond human ability”, according to the World Economic Forum, including in environments that would be normally unsafe for workers. As well as being able to complete complex tasks, intelligence driven advanced automation will also be able to real-time problem solve.
New-generation robots are incorporating voice and image recognition, increasing their ability to interact with humans. Collaborative robots or ‘cobots’, are starting to make an appearance, working side-by-side with humans in a shared workspace, carrying out monotonous or dangerous tasks – enabling humans to focus on other key aspects of their roles. Door opening solutions company Assa Abloy, for example, has deployed Active8Robots Sawyer cobots to carry out line loading, machine tending and packaging alongside its staff. The company maintains the cobots have improved productivity, quality and health and safety.
Another dynamic capability of AI and advanced automation is machine learning. This gives systems the ability to learn from experience, which means they are constantly improving. Machine learning enables manufacturing to be faster, flexible and scalable by providing predictive insight to manage everything from plant effectiveness to selecting optimal suppliers and gauging pricing against demand.
Working closer together
A key to economic growth is AI’s ability to manage capital efficiency, including managing labor requirements and machinery schedules to reduce down time and thus realize cost savings.
Robots, however, will not take our jobs anytime soon. But instead robots will be working more closely with us, allowing us to concentrate on jobs where specific human skills are required such as understanding context or innovating. It might surprise you, for example, that shoes still have to be laced manually in factories.
Mercedes Benz is ahead of the trend. It recently made some of its large production line robots redundant and replaced them with cobots. This move has seen the company increase its human hiring to focus on luxury car customization in particular. Why? Because re-training humans is much faster than having to re-program huge robotics solutions, making the cobots/human teaming much more flexible and agile.
The future of manufacturing
It wasn’t many years ago that manufacturing was in the doldrums. Increased efficiency through AI will create a much brighter future for global manufacturing. Integrating machine intelligence with human intelligence will in many cases generate more jobs on the product line that are more interesting and less mundane. As Satya Nadella, CEO of Microsoft recently wrote: “The beauty of machines and humans working in tandem gets lost in the discussion about whether AI is a good thing or a bad thing.” Manufacturing, it seems, has taken note.
Industry 4.0 promises to change manufacturing, supply chain and operations beyond recognition. It will drive deep changes in all functions and divisions of the “industrial enterprise”. Find out more here
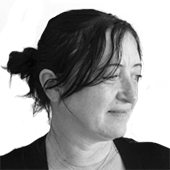
Jan has been writing about technology for over 22 years for magazines and web sites, including ComputerActive, IQ magazine and Signum. She has been a business correspondent on ComputerWorld in Sydney and covered the channel for Ziff-Davis in New York.