Fans of the Star Wars already know the difference between C3PO and R2D2: The first was a smart translation android while the second was a maintenance robot designed to collaborate with human colleagues.
Today we have another word for both ‘droids: ‘Cobot’, collaborative robots.
Germany’s Institute for Occupational Safety and Health (IFA) explains: “Collaborative industrial robots are complex machines which work hand in hand with human beings. In a shared work process, they support and relieve the human operator.”
Some claim the first cobot was deployed alongside humans when Denmark’s Linatex deployed a Universal Robotics machine on the production line.
What’s critical to understanding the nature of the cobot is that in all these cases the machines work in the same physical space as people, which means they will over time learn to integrate into human group dynamics. A research paper presented in 2013 at the 44th International Symposium on Robotics proposes further fusing of human/robotic learning models to develop risk-aware robots capable of selecting their own actions by learning within human teams.
With annual 50 percent growth, cobots have become the fastest growing segment of the industrial robotics market. Revenues are expected to reach $3 billion as soon as 2020. During the first half of 2016 alone, US vendors sold 14,583 robots to companies around the world, according to the Association for Advancing Automation (A3).
A3 claims US auto firms are leading the charge toward cobot deployment. U.S. vehicle production is up around 16 percent per year as a result, according to Bastian Solutions. These new robots are made by a range of companies, including: Universal Robots, Kuka Robotics, Fanuc America, and Rethink Robotics, but there are more.
From factory floor to operating theaters
Ford uses cobots at its factory in Cologne, Germany. They work alongside 4,000 human operatives, doing mundane, heavy-exertion tasks, such as attaching doors, painting vehicles, or fitting engines. Offloading these tough tasks enables human operatives to “use more of their creativity and their minds to take us to the next level,” said Bruce Hettle, VP manufacturing and labor affairs at Ford.
A Rethink Robotics’ Baxter robot works at custom moulding company, the Rudon Group. It does the jobs employees hate, such as the noisy and boring task of feeding scrap into recycling machines. The company has been able to improve productivity with these systems, as this in-depth report explains.
It would be an error to see cobots as limited to the factory floor. They are already being used to milk Swedish cows and keep some U.S. supermarket shelves stocked.
They are even being used in critical life or death situations. The Kuka LBR Med operating theater cobot helps surgeons during life-saving surgery, sawing bones, performing endoscopy’s and more.
Robots are also entering daily life. There is a growing body of research exploring how cobots may help elderly people live more independently. This may become necessary as population demographics change – there are already more elderly than young people alive in China and Japan.
While these collaborative systems will enable productivity gains, extend care budgets and take on the jobs employees hate, it’s quite clear they will replace many jobs.
Fastbrick Robotics has developed the Hadrian X, a robot capable of laying 1,000 bricks in one hour. It would take two human bricklayers a day to match that work rate. At AMA Plastics, five cobots have largely replaced human assembly workers, pushing experienced human workers into more demanding roles.
Impact on jobs
The World Economic Forum predicts robotic automation will result in the net loss of more than 5m jobs across 15 developed nations by 2020. The notion that more skilled and experienced workers will occupy more responsible roles in the new automated planet makes sense.
“We still have not made much progress on making dexterous hands for robots,” said Rethink Robotics CEO, Rodney Brooks. His company makes the Baxter and Sawyer cobots, which work alongside humans on production lines. While these robots are helpful in some tasks, the technology to fully replace human operatives just doesn’t exist yet, he argues.
All the same, as the technology evolves the range of tasks cobots can handle will inevitably expand. Human workers are already training their robot replacements in some industries. How will traditional HR functions need to respond to such change? More importantly, how will governments respond to the challenge of upskilling unskilled workers who have been replaced by machines?
To find out more about digitally transforming your business to help bolster collaboration, please click here
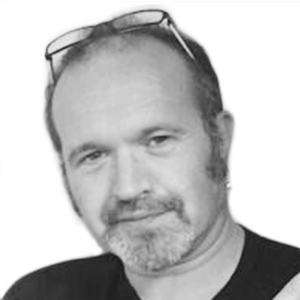
Jon Evans is a highly experienced technology journalist and editor. He has been writing for a living since 1994. These days you might read his daily regular Computerworld AppleHolic and opinion columns. Jon is also technology editor for men's interest magazine, Calibre Quarterly, and news editor for MacFormat magazine, which is the biggest UK Mac title. He's really interested in the impact of technology on the creative spark at the heart of the human experience. In 2010 he won an American Society of Business Publication Editors (Azbee) Award for his work at Computerworld.