Traditional manufacturing is in the throes of digital transformation. New technologies such as machine intelligence, cloud computing and connected devices are completely changing the way factories work, leading to what some commentators are calling the fourth industrial revolution.
(To summarize, the first industrial revolution in the 18th century was mechanical, the second revolution in the 19th was electrical, the third in the 20th century was automation through IT.)
Industry 4.0, the theme of Hannover Messe this year, is driven by the convergence of emerging and maturing technologies such as sensors, cloud computing, advanced robotics and artificial intelligence. And it’s not just smarter machines but how they interact with smart buildings, smart grids, smart logistics. One day it could lead to factories completely without a human workforce.
So how is Industry 4.0 impacting things?
One great example of this is London’s newest dock complex, London Gateway, where processes are heavily automated. Autostow, for instance, handles distribution, storage and retrieval across thousands of containers. Eventually the center should handle 3.5 million a year. This is a strong sign of how Industry 4.0 will transform haulage and transportation.
Other examples include a fleet of largely autonomous trucks from various manufacturers recently traversing Europe; Amazon continues to experiment with drone-based delivery systems; Uber makes no secret of its long range plan to replace drivers with autonomous vehicles.
Beyond logistics, automation is becoming smarter by the day. Just think about the automated systems building motors for Dyson vacuum cleaners, or the automated manufacturing of the Tesla Model S. They will need this to meet the demand for the 325,000 orders for its Model 3. Dassault Systems and CLAAS are creating more automated connected deployments of agricultural equipment. The semiconductor industry has been mostly automated for decades.
Automation is everywhere!
Affordable solutions
What’s changing is the cost. Robots are becoming affordable, albeit limited by the costs of maintenance, deployment and necessary supporting infrastructure. Not only this but new breeds of embedded mobile processor means the current crop can be upgradeable, capable and connected. They can even order the predictive maintenance they need before you know they need it.
Leading US companies including General Electric, Eaton, Molex, Microsoft and IBM will be among 250 to present solutions for networked industry in Hannover, where the Industrial Internet Consortium (IIC) will host a display for the first time. In the background technology giants are buying out swathes of artificial intelligence talent – over 20 AI firms have been acquired in the last three years by the likes of Google, Amazon, Apple, IBM, Yahoo, Facebook, Intel, and, more recently, Salesforce. The tech giants are investing in deep learning and neural networks, natural language processing, self-learning algorithms, AI personalization and machine learning.
Frost & Sullivan expects that in the very near future AI-controlled assembly and production lines will become the norm. They see big data and AI combining to create automated self-learning systems to replace existing infrastructure in production, distribution and beyond.
Self-learning machines
Until recently, industrial robots have been the epitome of point solutions: they are expensive, they need to be anchored to the floor, they need to be supported by humans, they need to be instructed and are generally only capable of manufacturing just one thing. Reprogramming (retooling) them to make a different item is complex, costly and fraught with challenge.
What analysts are excited about this time is that (more) intelligent machines using deep learning cognition systems such as IBM Watson will be able to acquire new skills to make or engage in new tasks. They will be able to build themselves.
This makes automated systems more flexible and responsive – these automated systems should in future be able to flip between manufacturing tasks as quotas are filled. They’ll never get bored. Never go on strike. Never take a vacation, and intelligent connected preemptive maintenance systems mean they’ll only rarely break down during a production run.
Employment 4.0
With so many implications across so many different industries Fortune magazine recently warned that “technological unemployment” could impact employability.
Forrester predicts that overall 7% of jobs will disappear and not be replaced due to automation technologies between now and 2025. “Our analysis suggests that, by 2019, 25% of all job tasks will be offloaded to software robots, physical robots, or customer self-service automation. For most workers, robotic colleagues will change the way we approach our daily jobs, requiring new methods of job training, management, financial reporting systems, and the like,” analyst JP Gownder explains.
However, at least one futurologist argues that very human skills such as empathy or story telling will be raised in importance, applying a human touch atop an automated infrastructure. While machines take over the task-focused challenges, soft skills like these will become more highly valued. The transition won’t be immediate, nor will it be easy.
Orange Business takes part in live demonstrations at Hannover Messe to showcase how we are helping to deeply integrate IT & IoT solutions in industrial applications.
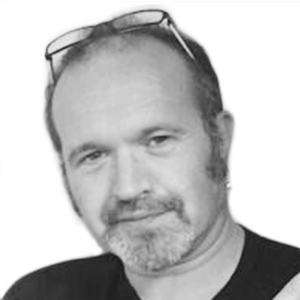
Jon Evans is a highly experienced technology journalist and editor. He has been writing for a living since 1994. These days you might read his daily regular Computerworld AppleHolic and opinion columns. Jon is also technology editor for men's interest magazine, Calibre Quarterly, and news editor for MacFormat magazine, which is the biggest UK Mac title. He's really interested in the impact of technology on the creative spark at the heart of the human experience. In 2010 he won an American Society of Business Publication Editors (Azbee) Award for his work at Computerworld.