Construction companies have been laggards when it comes to adopting new digital tools and technologies. And this is clearly affecting growth. According to McKinsey’s Reinventing Construction report, construction has only seen a 1% increase in productivity growth in the last two decades. This costs the global economy $1.3 trillion per year.
Some technologies already deliver tangible value for the construction industry. Building information modeling (BIM), for example, enables construction companies to create 3D digital representations of buildings. Benefits include cost and resource savings, increased efficiency and shortened project lifecycles, improved communications and project coordination, more opportunities for prefabrication and modular construction, and higher-quality results. BIM utilizes historical data and predictions to help companies plan and forecast more accurately, and in ways not possible using traditional blueprints.
How digital can make construction more connected
The Internet of Things (IoT) is also starting to play a big role in construction, with IoT-connected devices and sensors helping increase productivity, operational efficiency and site safety. Sensors can enable greater site visibility, which can mean improved productivity throughout a construction project lifecycle.
Examples of IoT solutions in construction include unmanned aerial vehicles (UAV), autonomous trucks, wearables and IoT sensors embedded in concrete during casting to gauge its compressive strength. IoT can help throughout the construction process and beyond: from design, manufacturing, engineering and procurement, to building operations and maintenance.
Augmented reality (AR) is finding its niche, too, from being used in 3D modeling and BIM to safety trials using digital twins. AR simulated scenarios can give construction workers a rich safety training environment and virtual walkthroughs of project sites that enable safe monitoring of work progress.
Robots at work
The same applies with robotics. Artificial intelligence (AI) company Doxel has designed a robot that traverses construction sites to check on the status of elements of ongoing building projects. It gathers data which is analyzed and used to spot potential problems at an early stage. Other robots are being used throughout the construction process, like long-armed bricklaying robots, which lay bricks three times more quickly than human workers. These robots can also utilize data to predict fluctuations in site environments in real time, such as movements from wind or vibrations.
At the beginning of a construction project, robots can be used for surveying and inspection of sites. Aerial drones or ground-based robots can gather data from construction sites and feed video back to control centers to give site managers insights into the state of a site before commencing building work. Robotics in construction is gaining momentum, with the robotics in the construction industry forecast to be worth $7.9 billion by 2027, at a CAGR of 23.3% from 2020 to 2027.
What is clear is that in the construction space, real-time data, IoT and other digital tools have the potential to connect infrastructure, from buildings to bridges, mines to tunnels, to monitor their status and enhance productivity, efficiency and safety.
The potential for 5G in construction
5G mobile connectivity has the potential to take digital transformation of construction to the next level. It can enable “augmented workers,” who are equipped with BIM, AR and other tools to help them be more informed and more productive on sites. 5G’s ultra-fast speeds and low latency can power new solutions like holographic building visualization, real-time design display and instantaneous access to data on sites.
It presents the possibility for a connected construction project in which materials are delivered to a site overnight and put into position by autonomous vehicles, ready to be used the following day. Then a digger operator wearing AR/VR goggles can work on the site using a 3D model of proposed excavations. Drones and sensors will enable site managers to monitor the work in real-time, removing the need for them to be physically present on site.
Supporting the construction ecosystem
Taken to its full potential, connected construction can create a dynamic, always-on construction ecosystem powered by data and analytics. The construction ecosystem is typically complex and unlike other industries. Every project is different, or a unique prototype, developed by teams of consultants, contractors and other suppliers who have possibly never worked together before and may never work together again.
A construction ecosystem, therefore, comprises different procurement systems that are responsible for different elements of the building project. Once you move past first-tier suppliers like the design consultants who work directly for the client, the ecosystem then splits into numbers of contractors, who in turn have supply chains of subcontractors and specialist suppliers.
On big, complex projects, responsibility and performance extends down the supply chain to numerous suppliers, into which the project management at the top of the chain has little visibility. Budget inaccuracies, approvals and subcontractor scheduling are often cited as key reasons for delays in construction projects, and it is easy to see why.
According to McKinsey, construction projects typically take 20% longer to complete than originally scheduled and can be up to 80% over budget. The average delay caused by supply-chain issues in construction is estimated to cost between 20% and 30% of the project’s value. Delays can be hugely expensive.
Data drives visibility and efficiency
Data will power a shift towards a more collaboration-based construction ecosystem that is better able to prevent these delays and minimize costs. For example, smart buildings and infrastructure that integrates IoT technology will increase the availability of data to be analyzed throughout the construction value chain to drive new efficiencies, such as performance-based and collaborative contracting.
Co-innovation will come into its own, too, as suppliers throughout the chain use BIM to create digital twins, which they can use to model layers of schedule and cost at earlier stages in a project. Data analysis and collaboration throughout the value chain also have the potential to transform traditional approaches to engineering, procurement and construction in general. A smart supply chain provides greater agility overall and enables more accurate decision making.
These technology innovations promise to transform the construction business model and the relationships in the value chain beyond recognition. Being connected digitally and leveraging data will allow them to establish a process of continuous improvement, powered by ecosystem thinking. Orange has expertise in this area, from our role as a master systems integrator on major smart city construction projects in the Middle East to our commitment to ecosystems for delivering value as part of our Engage 2025 commitment.
To read more about how digital technology is transforming traditional construction into connected construction, read this GlobalData Advisory Report on McConnell Dowell and their revolutionary IoT-enabled construction transformation project.
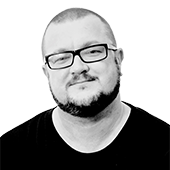
I’ve been writing about technology for around 15 years and today focus mainly on all things telecoms - next generation networks, mobile, cloud computing and plenty more. For Futurity Media I am based in the Asia-Pacific region and keep a close eye on all things tech happening in that exciting part of the world.